Producers get impartial assistance in joint effort against Teflon waste
PTFE (Teflon) is difficult to degrade and may be subject to a ban on PFAS. Three manufacturers are collaborating with FORCE Technology to recycle the substance and prepare for a possible ban.
Sintered PTFE – also known by the trade name Teflon – has several unique properties, including low friction, chemical resistance and temperature resistance. Therefore, we benefit from it in Teflon pans, but the substance is also used in industrial seals, among other things.
However, a problem with PTFE is that recycling is both difficult and expensive.
Collaboration on PTFE recycling in knowledge bridge project
Trelleborg, O.L. Seals, and Acoplastic are competitors in supplying seals and sealing solutions for industrial use. At the same time, the companies share a challenge in handling plastic waste from production in the form of PTFE/Teflon. A challenge so significant that it is difficult for the companies to handle on their own.
PTFE waste is currently largely sent to landfills because recycling is both complicated and expensive. Therefore, the three companies all agreed when FORCE Technology proposed they participate in a so-called knowledge bridge project to find solutions for greater sustainability and recycling.
Greater sustainability benefits everyone
“Sustainability is a goal for all of us, and it makes a lot of sense to collaborate on something that benefits the entire society. And it does when we reduce the amount of waste from the industry,” says Sara Krpovic, Materials Specialist at Trelleborg.
The project on PTFE recycling lasted six months, and the tangible result was a report focusing on the possibilities and challenges of PTFE waste, legislation and life cycle analysis.
Sustainability is a goal for all of us, and it makes a lot of sense to collaborate on something that benefits the entire society. And it does when we reduce the amount of waste from the industry.Sara Krpovic / Materials Specialist, Trelleborg
Pyrolysis and mechanical milling of PTFE waste
The two most obvious methods for recycling PTFE waste are pyrolysis and mechanical milling.
Pyrolysis
In pyrolysis, plastic waste is burned so that the PTFE breaks down into the components from which it is made, after which new PTFE polymers can be formed. However, there are no facilities for this demanding process in Denmark.
Mechanical milling
Another method is mechanical milling. Here, the PTFE waste is ground down to a sufficiently small size to recycle the material. Although this method is complicated, the project participants agreed to focus on and proceed with it.
A challenge is that PTFE often contains additives, such as bronze, which destroy the knives used for milling. Additionally, the task is to find the right size to mill the material.
Green accounting quantifies CO2 savings
Life cycle analysis was another focus area of the project. Here, FORCE Technology helped the three companies create green accounting for the recycling of PTFE.
Specifically, this involved calculating the potential CO2 savings from recycling PTFE. It turned out that the companies can save up to 8 kg of CO2 equivalent per kg of recycled PTFE. This figure is significant for finances, environmental impact and the companies' image.
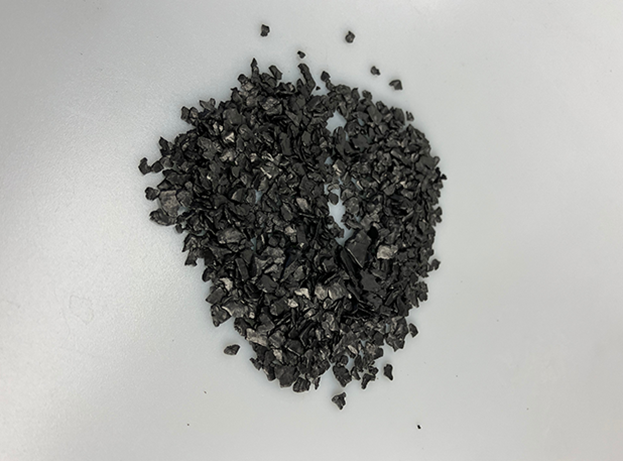
PTFE may be affected by PFAS ban
As widely covered in the media, the EU has proposed banning PFAS (perfluorinated and polyfluorinated alkyl substances). Under this large umbrella of substances, you also find PTFE, despite PTFE not being absorbed by the body like other PFAS substances.
While the EU opens for exceptions to the legislation, if PTFE is completely banned, there is, of course, no PTFE to recycle. Therefore, the industry is also investigating alternatives to PTFE.
Gaining knowledge about PTFE waste and sharing costs
In addition to concrete knowledge about, among other things, the possibilities for recycling PTFE waste, Trelleborg, O.L. Seals, and Acoplastic gained insight into what their competitors are doing in this area through the knowledge bridge project. Not with the aim of competing on sustainability, but rather to spar and lift each other to benefit both the industry and society as a whole.
Additionally, it motivates the companies to share the costs associated with, for example, mechanical milling and to spread the sustainability workload among more participants.
Competitor collaboration on neutral ground
Trelleborg found it natural to work with FORCE Technology on PTFE recycling, partly because the two companies have previously collaborated on a similar project.
“I like the way FORCE Technology is structured. It is not easy to get competitors to work together, but we are really on neutral ground here, and you have gathered many competencies in one place,” says Sara Krpovic from Trelleborg.
Journey towards better recycling continues
Finding the right method for milling and recycling PTFE waste is a complex task that cannot be solved in six months. Therefore – after the knowledge bridge project was completed – Trelleborg, O.L. Seals and Acoplastic have continued working on the highlighted possibilities.
The companies meet at least once a quarter to share progress and results in sustainability. In other words, the foundation has been laid, and a viable collaboration on sustainability has been established.
What is a knowledge bridge project?
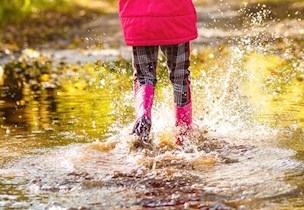
Prepare for a possible EU ban on PFAS
/Page
How do you know if PFAS is a problem for your company?
/Article
PFAS face possible EU ban from 2026: Time to assess its impact on your production value chain.
Test and analysis of plastics and composites
/Service
Ensure optimal material selection and design when working with polymers and composites.
Chemical analysis laboratory
/Facility
In our chemical analysis laboratory, we perform characterisation of all types of substances.