5 good reasons to have your product tested for electrical safety
Electrical safety testing is not just a legal obligation - it also leads to design improvements and good technical documentation.
Here are five important reasons to have your product tested for electrical safety before it goes to market.
1. Electrical safety testing is legally required for CE marking
Fulfilling the requirements of the relevant directives is a legal requirement to market products in the EU. Corresponding regulations apply outside the EU. Documentation that these requirements have been met must be kept in a technical file and made accessible for inspection during the period in which the product is marketed plus ten additional years. This technical file is required in order to prepare an EU Declaration of Conformity and to have your product CE marked.
Remember that there is always a legal obligation to ensure that your product is safe before bringing it to market. The legal requirements for electrical safety may be determined by the Low Voltage Directive, the Medical Device Directive (soon The Medical Device Regulation), the Radio Equipment Directive, the Machinery Directive (soon the Machinery Regulation), or other relevant directives. If a product is not already covered by other directives, the General Product Safety Directive (GPSD, soon GPSR) serves as a catch-all.
A common misconception is that there are no safety requirements for electronic products as long as the voltage is low enough. Indeed, some low-voltage products are not covered by the Low Voltage Directive, but in those cases, another applicable directive will still impose electrical safety requirements. Dangerous products may not be sold.
2. It minimises the risk of damage or injury when using electric or electronic products
An electrical safety test provides insight into whether or not one's product is safely designed, such that one can avoid or reduce the risk of the product being the cause of damage or injury to people, pets and property. The product must therefore be designed and produced in such a way that a potentially dangerous condition, in which an internal or external event may result in damage - that is, a hazard - does not arise.
Safety standards address hazards that may lead to damage or injury as a result of electrical shock, energy discharge, fire, heat, mechanical conditions (e.g., sharp edges, crushing, moving parts), radiation (e.g. RF, IR, UV, laser, sound, radioactivity), or chemical conditions (e.g. toxic materials, liquids, smoke, vapour).
3. Accredited electrical safety tests lead to greater safety
If a test is accredited, that means that the testing facility is subject to quality inspections (audits) from an authority and/or professional organisation (for FORCE Technology, these are DANAK and IECEE CB Scheme). The auditor verifies that a test is performed in a methodically correct manner, and that personnel are trained to perform the test, which includes ensuring that they are capable of making the many technical assessments that are part of the standards in use.
An accredited and certified test report from a testing facility like FORCE Technology is the best proof of proper, independent testing, and is therefore more useful to you than unaccredited test reports.
As a manufacturer, an accredited test report gives you a high degree of confidence that the report will be accepted by authorities in the various EU countries. Both in and outside the EU, many countries and regions require a CB Scheme certified report. With a report certified in accordance with the CB Scheme, a manufacturer can gain access to the global market.
4. It leads to improved technical documentation
The results of an electrical safety test are recorded in a test report, which is collected in the product's technical file. The technical file must be made available for inspection by authorities while the product is available for sale, and for ten additional years after that.
A significant part of an electrical safety test is a design documentation review. Often, far less than half of the testing period is spent actually performing tests. Most of the time is spent examining the product and its documentation.
For this reason, manufacturers virtually always find that their technical documentation is significantly improved when they perform electrical safety tests. This gives you the confidence that, upon request from national authorities and in the event that any damage or injury should occur, you have taken the appropriate steps to make your product safe and secure.
5. It leads to design improvements
In the course of electrical safety testing, many businesses find that they develop new, detailed technical knowledge of their own product. Initially, the manufacturer simply becomes certain of how to make the product safe. Gradually, however, as the approval project continues on, the product developer often gains insight into their own product, creating opportunities to optimise the product's design. In this manner, a foundation for the growth of new ideas and general improvements is created, while the product is made legal and safe.
Contact us if you need to have electrical safety testing performed. FORCE Technology offers do-it-yourself-test, technical guidance, interpretation of standards specifically for your product, and help to make the testing process as easy as possible, as well as accredited testing and test reports that are IECEE CB Scheme-certified.

Electrified classic cars gain market access
/Case

Lab: electrical safety testing of electronic products
/Facility
Safety testing of electronic products for compliance with regulations and standards.

Electrical safety test
/Service
There are legal requirements to ensure that electrical and electronic products are safe in use.
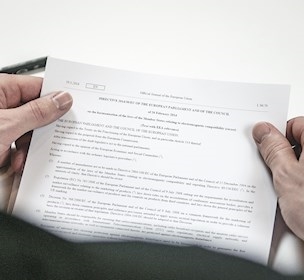
Accredited product certification
/Service
Product certification is mandatory for many product types and the ultimate mark of quality.