System or module level testing of electronics?
Scalability is a great tool to ensure the most efficient test when products with electronics are to be tested for reliability.
How is your product tested? There are many answers to that question, which all are influenced by factors like budget, time pressure, and availability of testing possibilities.
However, there might also be regulations and standards dictating the answer.
Furthermore, it might be an advantage to build on the required quality requirements in order to obtain and document an increased reliability and robustness.
Some companies have a long and integrated history with reliability tests and take high reliability into account right from the design phase until complete installation, while other companies have just started the journey towards higher reliability. However, most companies can – regardless of their maturity – improve their reliability strategy.
Focusing on the right strategy
With the attainment contract Proactive Paradigm for Electronic Product Reliability (PPEPP) FORCE Technology focusses on developing a paradigm that can assist Danish companies in finding the right reliability tool that increases the reliability of their specific products in the most efficient way.
There is a wide range of testing possibilities to ensure the reliability of a product, but keeping the bottom line in mind, it is important to choose exactly the tool or the test that is most effective as to the reliability.
Besides, continuous technological progress and approaches entail that new testing methods emerge, become more common or are available at quite different scale levels. Therefore, part of this PPEPP paradigm focusses on developing a tool to illustrate at which level you should/can test a product.
The individual company’s motivation might be to save time by reducing the number of reliability tests by testing at a higher level and thus gather more elements together in one single test, or by replacing a complicated and expensive test at system level with a simpler test of a central component at a lower level.
Scalability
This scalability of reliability tests is by far trivial and there are no secure methods for breaking down a complete system test to test requirements for component parts of a big system. The approach to the problem is based on decades of experience with reliability tests within climate, mechanics, and electromagnetic compatibility (EMC).
Some would call it System Engineering, common sense or a part of an intelligent test, but as a whole the purpose of the tool is to illustrate advantages and disadvantages by testing at a given level, to identify the components/modules with a high risk of failing, and to identify factors both internally and externally for the product.
A hypothetical example could be a vehicle – a complex system with high reliability requirements. If this system is split into suitable levels from the smallest to the largest, it could be component - printed-circuit board – module – subsystem - system. The further down the levels we move, the greater the number of elements at each level will be.
If the test is exclusively performed at the lowest level, the scope of testing becomes inefficiently large. Meanwhile, there is no guarantee that the vehicle will start when pushing the button. However, if testing exclusively takes place at the highest level, there will be no information about the margin of error for the individual components or modules. In turn, the risk of testing only at the highest level is big as such a test would probably take place at the end of a development process and if a critical error is not found until that stage, it may have catastrophic consequences. Who wants to test-drive a car where nothing has been tested in advance? There must be something in between.
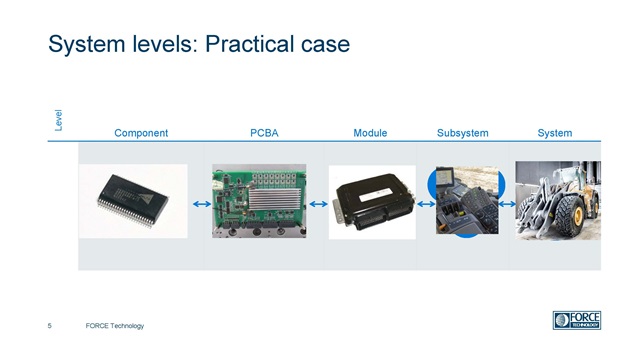