Sika Marine helps improve acoustics on ships
Low noise and vibration behavior in ships are important to ensure that passengers have a pleasant journey. Sika Marine, in collaboration with FORCE Technology, is working to enhance onboard acoustics through innovative noise reduction solutions.
Noise- and vibration level vital for passenger satisfaction
Today, one of the most important issues for vessels is low noise and vibration behavior. This applies especially for cruise ships and luxury yachts. A cruise ship with poor reputation regarding noise will often result in complaints from passengers, leading to loss of sales. Effective noise control enhances passenger satisfaction and protects a ship’s reputation.When building a new ship, the use of noise and vibration prediction tools in the design and building phases can minimise the risk of noise and vibration problems. Furthermore, a noise prediction can ensure that the vessel will comply with specific noise criteria and give the shipyard or shipowner an idea of the extent of necessary noise reducing measures already at the design stage.
Noise reduction measures
Sika Marine, a leader in marine floor solutions, partners with FORCE Technology’s acoustics team to measure and reduce structure-borne noise on ships.Tony Jenkins, Key Account Manager in SikaFloor® Marine says:
“The practice for producing measurable values for airborne and impact noise reduction on ships is well established and the performance of these various systems can be quantified. However, there is currently no ISO standard for measuring structure borne sound and damping properties for marine floors and bulkheads. Working with FORCE Technology's acoustics team, we are now able to document this reduction of magnitude and provide this information to the acoustics experts involved in the design of vessels.”
Predicting noise and vibration
As an outcome of DELTA’s merger with FORCE Technology, we can now offer a wider range of services to our maritime customers – also within noise and vibration on ships. We can predict excitation forces from the propulsion system using propulsion hydrodynamic and computational fluid dynamic capabilities. The structure borne noise source strengths from the other main noise sources, e.g. auxiliary engines’ main compressors, and ventilation units are used as excitation forces in the noise prediction model.By combining vessel layout data with noise source analysis, we can predict and compare noise levels, allowing for better design decisions and effective noise reduction strategies. Based on the results acoustic noise reducing construction e.g. floating or vibration damped floor constructions, can be introduced to fulfil the noise criteria.
In order to do this, knowledge about the noise reducing properties of these constructions is necessary for prediction of the expected noise levels with these constructions applied.
Structure borne noise insulation
The noise reducing properties of marine floors can be measured in our acoustical laboratories at the Technical University of Denmark (DTU), in which we can install a test section of a ship deck (10 m2) and perform different acoustical tests. The sound tests are the measurement of sound insulation properties and impact sound insulation properties according to ISO 10140.
However, in most areas of vessels the structure borne noise insulation properties are the most important parameter for the noise. These properties are measured using a dynamic exciter as an excitation force on the mounted test deck. Measuring the parameters with and without the noise reducing floor, the effect of floor systems can be determined.
Furthermore, FORCE Technology undertakes independent noise and vibration investigations e.g. checking for conformance of noise and vibration requirements, trouble-shooting assignments for investigation of noise or vibration problems. These investigations are designed to find the course of the problem and to recommend potential solutions using vibration or noise control measures.
Want to learn more? Explore how FORCE Technology helps businesses tackle sound emissions challenges in our case study on Haarup Maskinfabrik.
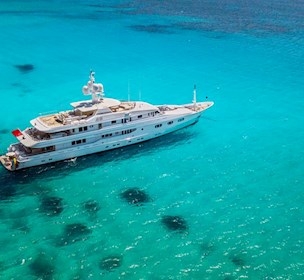
Marine noise and vibration
/Service
Acoustics, noise and vibration are key comfort parameters for ships.
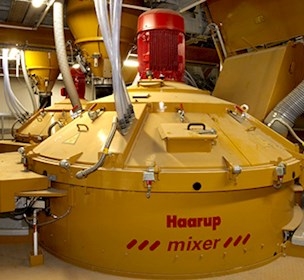
Haarup Maskinfabrik
/Case
Sound emission measurements of concrete mixer documents machine safety to the authorities.
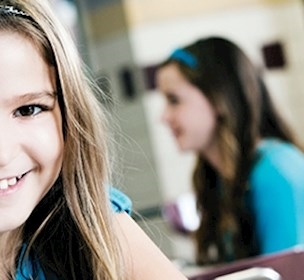
FurnX noise-dampening school desks
/Case
FORCE Technology measured the impact noise of four desk surfaces for the use of e.g. schools.