Screening metallic materials for hydrogen embrittlement minimises the risk of damage
Avoid the catastrophic damage that results from the collapse of load-bearing components by introducing hydrogen embrittlement screening in the design phase of metal components for critical structures.
High-strength steel is commonly used in critical structures like bridges, Power-to-X facilities, and offshore constructions like wind turbine foundations and sheet piling walls in harbours. Many project owners prefer high-strength steel because of its hardness and savings on required steel compared to lower strength materials, saving money.
However, the hardness of high-strength steel can also be a disadvantage, as the steel may be more sensitive to hydrogen. Hydrogen embrittlement can quickly lead to catastrophic failures.
Introduce screening in the design phase to minimise the risk of hydrogen embrittlement
The occurrence of damage caused by hydrogen embrittlement continues to emerge. The damage typically occurs rapidly and without warning. Hydrogen is often found in high-strength steel, including structural members such as bolts - and bolts are often crucial to the quality and safety of a structure.
The fact that a bolt meets the hardness requirements for a given application does not mean that it cannot fail. And once one bolt has cracked, what about the others? Will they fail soon, too?
Since many components, such as bolts and other structural components, can fail due to hydrogen embrittlement, we recommend testing these critical components early in the design phase of a critical structure. This further reassures the project owner that the structure will withstand what it must for its intended lifetime.
Hydrogen embrittlement screening also minimises the risk of damage that could require expensive repairs or even lead to fatal consequences.
How does hydrogen embrittlement occur?
There are several issues associated with hydrogen embrittlement risks that you should be aware of. Hydrogen embrittlement can occur when a metal object is exposed to hydrogen, such as in the following contexts:
- Welding—focus on hardness in the heat-affected zone
Moisture and inadequately cleaned metallic materials are the best-known sources of hydrogen in welding contexts. Hydrogen often collects in the heat-affected zone, and hydrogen-induced cracking can develop for up to 48 hours after welding. It is also important to avoid increasing the material's hardness significantly during welding, as this increases its hydrogen sensitivity.
- Corrosion processes during exposure to seawater
A structure placed in seawater can corrode, releasing hydrogen. The hydrogen can then diffuse into the steel, creating a risk of new or accelerating propagation of hydrogen-induced cracks. These can then lead to breakage.
- Manufacturing and surface treatment processes
Hydrogen can also be introduced into steel during the manufacturing process itself, both when raw materials are transformed into steel and when surface treatments are applied to finished components, as in hot-dip galvanisation. Cleaning components in substances like hydrochloric acid also releases hydrogen that can diffuse into the steel and accumulate there.
- Direct contact with hydrogen, such as in power-to-X facilities
If the metallic material will be directly exposed to hydrogen, such as in a gas pipeline or a power-to-X system, it is important to use materials designed to withstand this in the design.
The risk of hydrogen embrittlement increases when a part is under load
Problems related to accumulated hydrogen do not appear until the parts are subjected to mechanical stress. Consequently, tensile stress, high pressure, or high temperature may result in breakage. A delayed fracture can occur within 72 hours after a bolt is subjected to tensile stress.
One way to prevent damage is to test bolts before installation using the ISO 15330 standard, entitled "Preloading test for the detection of hydrogen embrittlement". Subsequent fracture mechanics calculations can also qualify that the construction can withstand hydrogen exposure under the specific pressure, as the risk of hydrogen embrittlement increases with higher concentrations of hydrogen and by increasing the pressure in the pressure-bearing equipment.
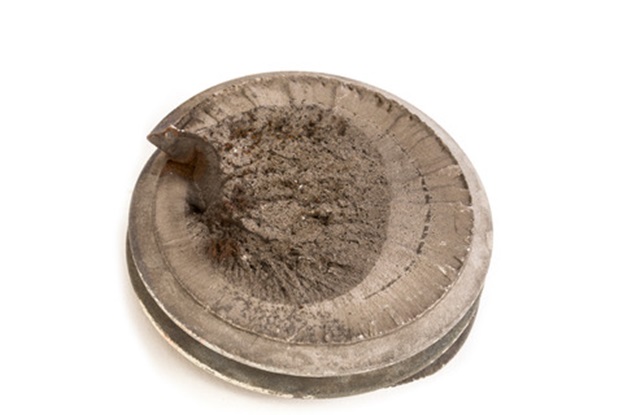
In connection with the transport and storage of hydrogen in pipelines and pressure vessels, additional demands are made on materials and their properties in hydrogen. Depending on which standards and calculation methods are used, one must both examine the properties of the materials and document their use with fracture mechanics analyses.
At the same time, the fracture mechanics tests will qualify the material and the fracture mechanics analyses can be used to determine inspection intervals during the life of the pipeline, which reduce the risk of unwanted accidents.
Fracture mechanics calculations can deliver large savings
With the test results in hand, we can perform fracture mechanics calculations of critical error sizes, ECA (Engineering Critical Assessment), which can qualify your designing your plant or pipeline with a reduced material thickness.
Reduced material thickness means both reduced material costs but also saved man-hours when, fx thinner pipelines have to be welded together.
This way, you can save money on the construction in the design phase, while you have documentation that it can withstand the influence of hydrogen at a specific pressure.
The calculations can be used both for the construction of new pipelines and existing pipelines to be used for another medium, eg hydrogen instead of natural gas. In existing pipelines, we document the remaining life of the pipeline with the new medium and the limit value for stress corrosion.
Put your components through a step-loading test in hydrogen at our testing facilities
Hydrogen embrittlement is enabled by a critical combination of:
- Stress
- Environment
- Material sensitivity
We can test your components at our HPHT testing facilities by placing them in a hydrogen-rich environment and gradually increasing the mechanical stress (step-loading) on them until they fail.
Our testing set-up is based on the foundations of ASTM F1624, "Standard Test Method for Measurement of Hydrogen Embrittlement Threshold in Steel by the Incremental Step Loading Technique".
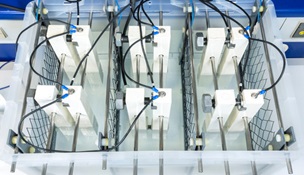
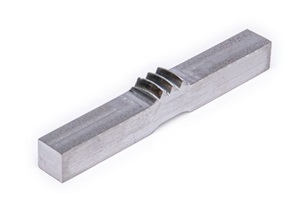
Gradually increasing mechanical stress in a well-regulated, hydrogen-rich environment offers a clear indication as to whether a material's characteristics fall within the limits of acceptability for hydrogen embrittlement based on requirements and standards, considering the harsh, aggressive environments that components may be subjected to.
We test 6–9 specimens at once, and the process takes about a month.
With proper test equipment, service life and inspection intervals can be calculated
FORCE Technology has equipment to test materials' risk of hydrogen embrittlement at different concentrations of hydrogen, at pressures up to 200 bar and temperatures varying from -20 to 200°C.
Tests are performed according to ASTM E1681 which follows recommendations in ASME B31.12 and ASME VIII div. 3 KD 10, for determining a material parameter, critical stress intensity factor, for when hydrogen embrittlement occurs in a sharp flaw in a material.
The obtained material parameter can be used to determine critical error sizes in pressure-bearing components, as well as calculate crack growth, lifetimes and inspection intervals.
Do you want more information?
Contact us to find out more about having components tested and ensuring that your metallic components will not fail due to hydrogen embrittlement.
If damage or an incident has already occurred, we can also help you determine the failure cause through RCA (root cause analysis), allowing you to avoid recurrence in the future.
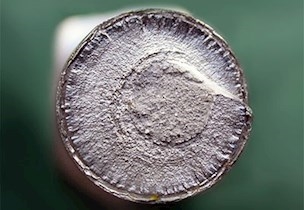
Article
Avoid the bolts becoming the weakest link!
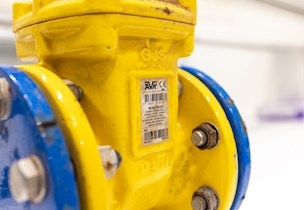
Case
AVK tests valves for use in hydrogen
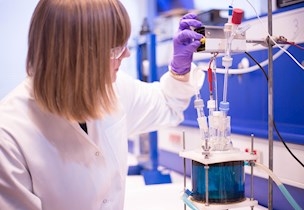
Standardised tests and special procedures - materials
/Service
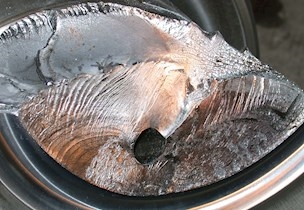
Failure and damage investigation
/Service
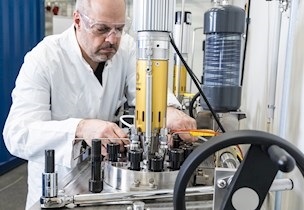
Facility
HPHT testing in realistic environments
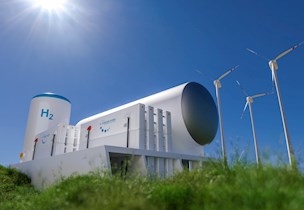
Facility