5 tips for development of reliable and robust electronic products
Development of electronic products requires a 360-degree approach to reliability and robustness where all relevant failure mechanisms and external conditions are accounted for.
"You can't test your way to reliability" is a statement most people would agree to. FORCE Technology has many years of experience dealing with situations where the opposite strategy has gone wrong. Reliability must be designed into the product from the beginning. We have identified the following five tips to increase reliability and robustness of new electronic and mechatronic products:
1. Define a requirements specification, standards, and success criteria
A powerful requirement specification known to all project members and communicated to any subcontractors is an important tool for developing reliable, robust products that fulfil relevant requirements from authorities, customers, and the company itself. In the specification phase, it is crucial that resources and skills are in place to ensure that the requirements are verifiable or testable. Large amounts of time and money can be saved in the development process by choosing unambigious success criteria and specific procedures in the standards for every requirement in terms of:
- Hardware
- Software
- Mechanics
- Lifetime
- Use environment.
2. Develop a product mission profile
In the specification phase, a mission profile for the product should be prepared. Establishing the product's functionality, lifetime, and environment while in transport, storage, and operation are prerequisites for a reliable electronic design. This is the product's mission profile. To determine the influence of the conditions in the mission profile, the following mechanical enclosure characteristics must be established:
- Physical size
- Heat dissipation
- Temperature limits for operation, storage, and transport
- Temperature changes during operation, storage, and transport
- Cooling requirements
- EMC conditions
- Mechanical robustness (forces, vibration, and shock)
- Protection from humidity, dust, and water.
3. Define reliability targets
It is very important to have well-defined reliability targets for the product, known to the developer, the sales organisation, and the customer. Examples of reliability targets might be:
- The percentage of the products produced, which are expected to function after a given period of time
- A rate of failure under a certain level over a certain period of time.
4. Conduct a design review
It is preferable to conduct several design reviews throughout the process, as you reach milestones. These reviews may have different focuses, such as
- Software architecture, design, and code (which can be reviewed as a walk-through)
- Electrical diagrams (component selection, component derating, lifetime, and EMC robustness aligned with the product mission profile)
- Mechanical and thermal design.
5. Perform early pre-testing
If the product fails in verification testing or accredited testing, this will lengthen the development process and require new tests. Large amounts of money and development time can be saved by focusing on critical areas early on. Below are some tests that we have found to be highly valuable if conducted early in development:
- EMC immunity and emission testing
- Resonance search (vibration)
- Drop testing
- Cyclic humidity with condensation
- Corrosion testing
- High temperature testing
- Rapid temperature changes.
The right test for the job
No one test fits every purpose. Figure 1 tells a story about how the functionality of a product is typically degraded by environmental conditions over time. It also shows how tests can be divided into various test types, including function testing, environmental testing, and reliability testing using HALT (Highly Accelerated Limit Testing) as a particular case of environmental testing.
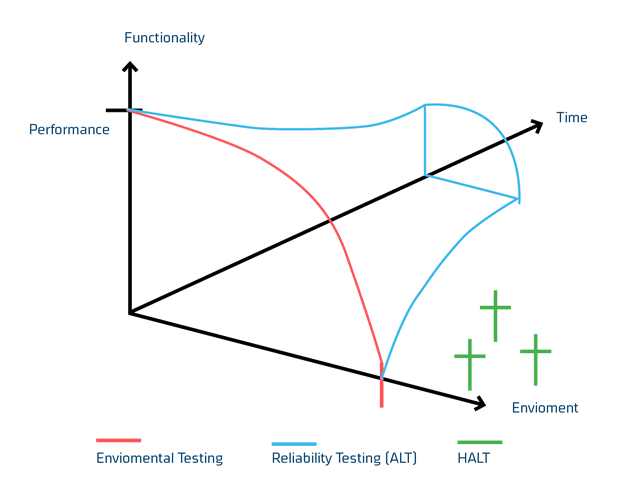
Using the 360-degree approach, a mission profile, and a requirements specification, the relevant environmental tests for a given product can be defined. Traditionally, environmental requirements are broken down into categories such as these:
EMC: Emission and immunity (radiated and conducted), ESD
Climatic: Temperature, humidity, water, air pressure, sunlight
Mechanical: Vibration, shock, falls, shearing, bending, impact
Chemical: Sweat, salt mist, cleaning liquids
Other: Flora (fungi), fauna.
The 360-degree approach is important to ensure that all relevant aspects are covered, with nothing slipping through the cracks — even when some aspects arise out of regulatory requirements, while others arise out of a desire for reliability and robustness to ensure customer satisfaction while limiting service- and guarantee-related expenses.
The purpose of an environmental test can vary significantly, depending on whether it is a design verification test, an approval test, an accelerated lifetime test, or a robustness test. Design verification tests and approval tests aim to simulate environmental conditions the product will be exposed to during its life cycle, while accelerated lifetime and robustness tests aim to stimulate relevant failure mechanisms.
HALT: not just traditional thermomechanical testing
HALT (Highly Accelerated Limit Testing) is one of the most efficient tools for finding potential weaknesses in a product before it is released for the market. It can be beneficial to perform HALT several times throughout the development process for electronic products, as it can save large amounts of time and money. Often, only one or two days of HALT are required. Early in the development phase, HALT can even reveal potential software timing issues. When a new product in a mechanical enclosure is fully operational, with all functions working, a traditional thermomechanical HALT is performed. The motto is "find the five weakest points, fix them, and the product will be significantly more robust/reliable". When a failure requiring modification has been found in a PCB layout, a traditional thermomechanical HALT can be performed on all the other functions in a single day.
But HALT is about much more than just traditional thermomechanical conditions. Again, the 360-degree approach is fundamental in ensuring that we do not simply reach instinctively for thermomechanical HALT in our testing toolbox. We must also consider whether or not all the weaknesses we can — and cannot — imagine in the product could be stimulated by other conditions. Thus, tests like EMC-HALT in a reverberation chamber, HACT (Highly Accelerated Corrosion Testing), or something entirely different may be required. The philosophy of HALT is about finding relevant weaknesses, regardless of the conditions required.
We suggest considering these points when determining the relevant HALT condition(s):
- Experience — your own or others'
- Top 10 lists of failures in similar products on the market
- Technology — what failure mechanisms are expected
- Literature; e.g., SPM-174: Advanced HALT.
Testing facilities for 360-degree reliability and robustness
A 360-degree approach to reliability and robustness, taking into account all relevant conditions, is crucial to seamless products that fulfil expectations from the market and from customers.Our facilities are designed just for this, with a long-awaited expansion of the EMC testing laboratory to include climatic and mechanical testing equipment and capabilities (see photos 1, 2, and 3).
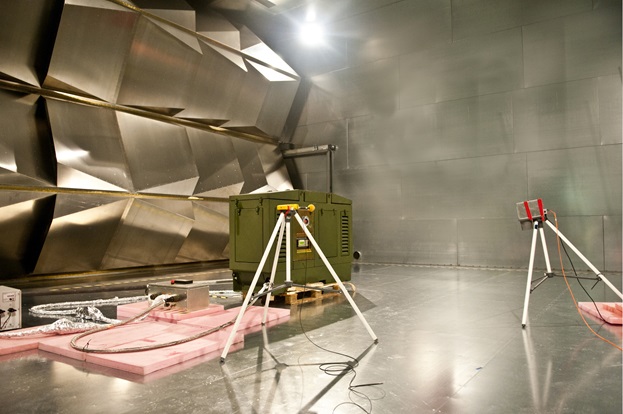
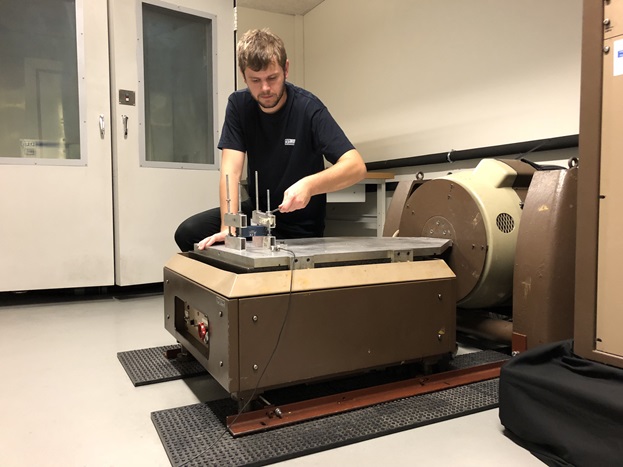
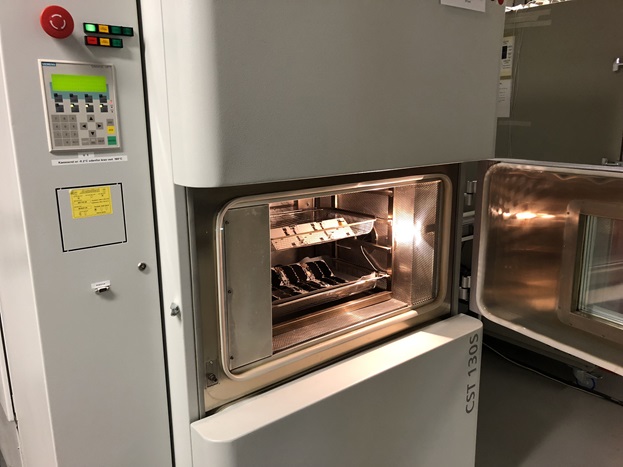