Reduce operational uncertainty in large volume gas transfers
Importance of managing fiscal risk in large volume gas custody transfer.
Industry best practice for setting gas measurement uncertainty
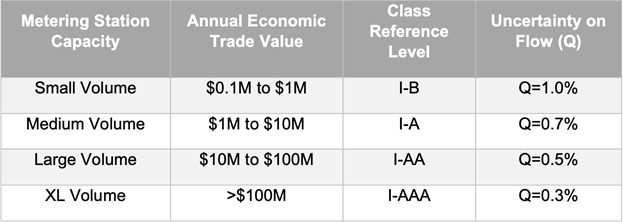
Their guidelines, shown in Figure 1, recommend uncertainty limits based on annual economic trading value.
For an economic trading value up to $100M, the recommended uncertainty limit is 0.5% of the flow. This helps keep the customer’s financial exposure around half a million dollars annually at large volume stations. For system uncertainty budgets, the American Gas Association (AGA) suggests a limit of 1.0%, or about $1M in overall uncertainty for large metering stations.
These recommended budgets are based on balancing the cost of advanced measurement solutions with the financial implications of uncertainty, while also accounting for current measurement technology capabilities, prices, and uncertainties.
For smaller volumes with lower annual economic risk, less robust technologies such as ultrasonic meters with fewer paths and no redundancy may be acceptable. However, in large volume gas custody transfer applications, the high cost of uncertainty demands that state-of-the-art technologies evolve to meet stricter uncertainty budgets.
Three prevailing large volume gas measurement technologies
Most pipeline operators aim for an operational measurement uncertainty of less than 0.3%, but achieving this is challenging, even with custody transfer-rated meters. Meeting this threshold often requires addressing limitations in piping design and meter technology. Even then, this uncertainty is typically only achieved when the highest accuracy flow meters operate in ideal conditions.
- Differential pressure (DP) meters: First introduced in the 1930s, DP meters are available in various sizes and excel in harsh environments. The orifice fitting, a type of DP meter, was the most common type used for custody transfer until the 1980s, when turbine meters gained acceptance for custody transfer, particularly in cleaner downstream environments like gas pipelines.
- Turbine meters: Known for their high accuracy, repeatability, and broad turndown ratio (the range of flow velocities they can measure accurately), turbine meters are flexible for operational changes such as flow rate fluctuations. These meters are now widely used for gas custody transfer.
- Ultrasonic flow meters: Though ultrasonic measurement technology existed since the 1960s, it wasn’t widely accepted for gas custody transfer until the late 1990s, with the publication of AGA 9. This report provided clear metrological guidelines, leading to global adoption. Early ultrasonic meters faced criticism due to poor designs and misunderstanding of the technology. However, advancements in path configurations, processing speed, digital signal processing (DSP), and software have significantly improved performance, diagnostics, and usability.
The rise and evolution of ultrasonic flow meters
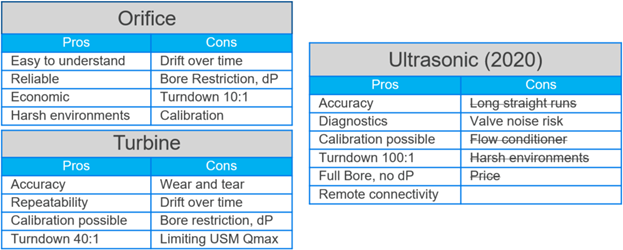
Minimizing the effect of process disturbances on operational uncertainty
The problem of common mode error
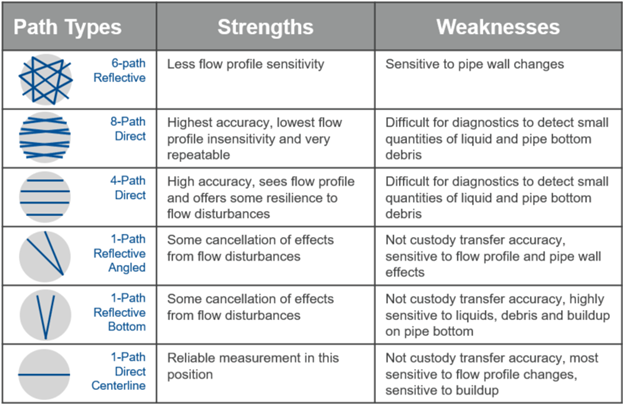
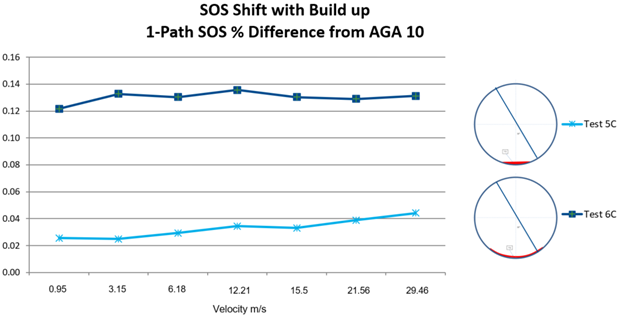
New test qualification for limiting operational uncertainty
While traditional metrology standards focus on calibration and installation effects, they fail to account for real-world operating conditions. DNV GL’s new test qualification addresses common process conditions that impact operational uncertainty. These conditions, found at field sites globally, were used to design test criteria that better reflect the uncertainty seen in the field.
For example, reflective and direct path meters show opposite flow error biases, helping to detect process disturbances early. In contrast, liquid or buildup contamination requires the comparison of speed of sound (SOS) between different meter types and paths to identify issues.
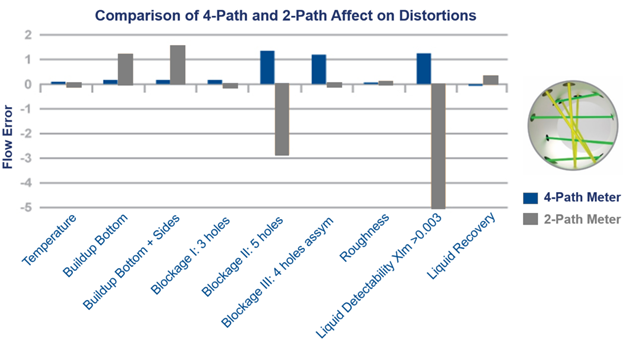
An ideal combination for minimizing operational uncertainty
With the evolution of technology, ultrasonic meters now offer more paths, such as 8-path meters. These advanced meters improve measurement accuracy, maintain high performance despite upstream disturbances, and reduce the need for lengthy upstream piping or flow conditioning.
For example, Emerson’s Daniel 3418 meter, combined with the Daniel 3416, offers a robust combination for maximum accuracy, repeatability, and process intelligence. These meters provide high reliability even under challenging conditions, offering operators an optimal solution to minimize operational uncertainty.
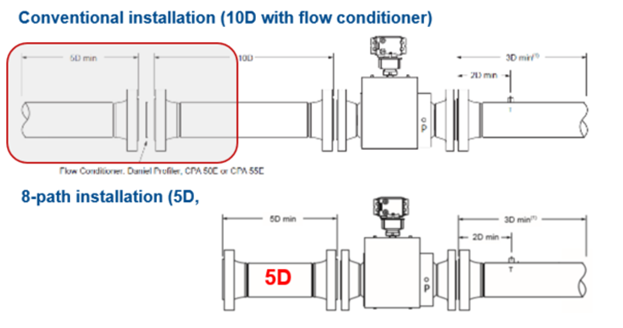
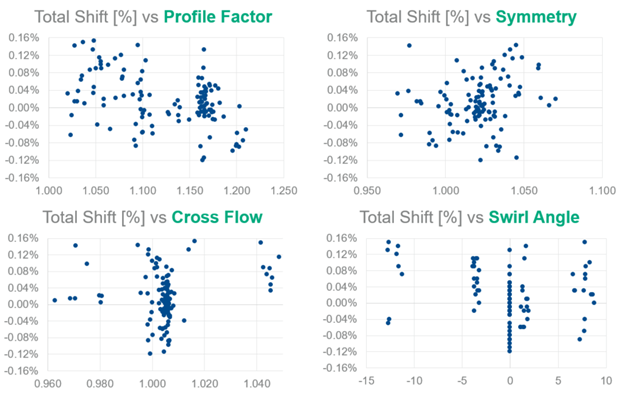
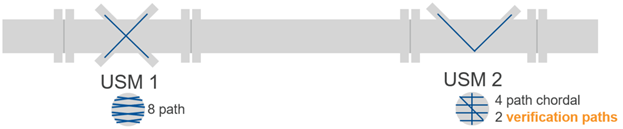
Looking ahead: What's next?
The rapid evolution of ultrasonic technology has expanded its use beyond clean, dry gas environments. Ultrasonic meters are now widely accepted in applications like wet gas, corrosive environments, biogas, coal bed methane, LNG, and more.
The development of condition-based monitoring systems, machine learning, and artificial intelligence is poised to further enhance the capabilities of ultrasonic meters. With increased investment in IoT infrastructure, operators are now able to move diagnostic data to the cloud, unlocking new potential for process management, system uncertainty reduction, and predictive maintenance.
As these technologies continue to mature, it’s clear that ultrasonic metering solutions are not only advancing in robustness but also intelligence. With this progress, they may soon exceed the long-term repeatability of turbine meters, marking a new era in gas custody transfer technology.
Interested in this topic? Sign up to receive news and articles about gas flow calibration or read more about calibration here.
Related content
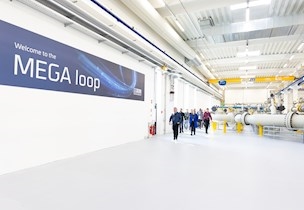
MEGA loop inaugurated
/News
EMCO Controls' choice for accurate calibration
/Case
Precise measuring instrumentation is imperative in the global custody transfer infrastructure.
High-pressure calibration of metering lines
/Case
Emerson are left with a verification that guarantees their customers accurate custody transfer.
MEGA loop revitalised
/News
The proportions of the MEGA loop will open up new possibilities for calibrating long meter systems.
Uncertainty explained: Uncertainty budgets
/Article
Which factors are important to know and address when working with uncertainty budgets?
Uncertainty explained: How is a calibration result reached?
/Article
In order to understand uncertainty calculations, it is necessary to know how a calibration result is reached.
Uncertainty explained: How to calculate laboratory CMC?
/Article
What is CMC, and how does it involve the uncertainty of the laboratories?
E-guide: Understand calibration certificates
/Article
Learn how to read, interpret and understand gas calibration certificate with this e-guide.
Uncertainty explained: Class half meters
/Article
Most laboratories in the world don’t have uncertainty levels adequately low to perform accredited calibrations of a class half meter. How does this affect the gas metering industry?
5 arguments for re-calibration of gas meters
/Article
Why perform re-calibration of gas meters? 5 gas industry professionals share their opinion.
8 things to remember when shipping gas meters to a calibration facility
/Article
We have gathered our best tips to successful shipment of your gas meters.