Strength analysis of welded structures
Strength analysis of welded structures may safeguard you against breakdowns and failure. We work according to current standards so that your structure lives up to legislative requirements and regulations.
Welding changes the material's mechanical properties
Welding exposes the material to very high temperatures, followed by cooling. The mechanical properties in the heat-affected zone (HAZ) are thus changed, and the structure will creep and deform. Furthermore, the weld is left with residual stresses that lie around the yield strength of the material.
When dimensioning welded structures, you have to consider these factors, for both statically and dynamically loaded structures.
A weld does not necessarily have the same mechanical properties as the base material, and it is therefore important that the weld is designed correctly to prevent subsequent fractures in the weld.
The static strength of a weld depends on several factors such as:
- Partial or full penetration
- Size of the throat thickness
- Strength of the weld metal
- Impact strength.
The biggest challenges with welds are typically fatigue and thus service life. Most fatigue cracks in structures initiate in a welded joint. The fatigue life of welded joints depends on the stress spectrum at the weld, the weld detail design and a possible subsequent heat treatment.
Calculation of strength ensures the service life of structures
We provide advice on and determine the strength of welded joints both for static and fatigue-loaded structures. For statically loaded structures, we are able to determine the static strength of a weld and design the weld to achieve optimal size and strength in compliance with the requirements.
Our experience also includes welded structures at low temperatures, where it is necessary to assess the impact strength of the weld to avoid brittle fracture.
We have wide experience in assessing weld details in order to determine fatigue life and inspection intervals. As to fatigue life, we always include a certain fracture probability. It is therefore possible to determine the fatigue life of structures with lower safety factor if you perform regular inspections of the welded joints.
Simultaneously we can give advice on weld detail design with the purpose of increasing the service life of your structure, before a fatigue crack initiates and creates the root of a subsequent fatigue fracture.
If you do not know your stress spectrum, there are ways of determining it. We offer finite element analyses (FEM) on the structure and, by this method, either determine nominal or hot spot stresses in the weld. If your structure has already been finalised, we offer strain gauge measurements to determine the actual stress spectrum and, by this, calculate the remaining fatigue life of the weld.
For welded structures, we also offer an estimate of the extent of expected deformations after finalised welding, in the form of creep, angular misalignment and deflections. Furthermore, we can tell you how the deformations can be minimised, to prevent you from ending up with a too short or a very out of shape work piece after finalised welding.
We apply current standards in our calculations, and you are thus certain that your structure is correctly designed with regard to strength and fatigue life.
Contact us to get a strength analysis to confirm the strength of your structure and remaining life span.
Services
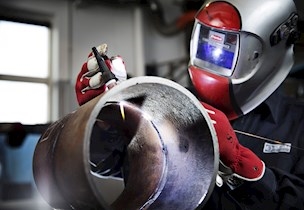
Welding consultancy – Improve weld quality
If you need to optimise and improve welding processes or find the reason for welding defects.
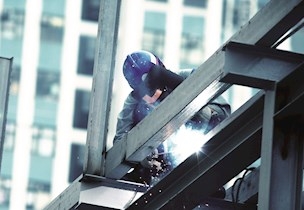
Strength analysis of welded structures
Strength analysis of welded structures can protect you from failure and accidents.
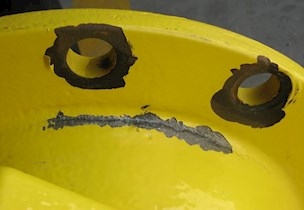
Materials selection and corrosion protection
The correct materials and optimal corrosion protection gives your product a longer service life.